In Kozhikode, the craft of making an uru or dhow (traditional wooden ships) is a continuation of a 2,000-year-old legacy. Today, Beypore, located near the mouth of the Chaliyar River, where it flows into the Arabian Sea, is home to one of the last few surviving boatyards. Commissioned by a businessman from Qatar, two urus were built here over the past five years on a grassy stretch surrounded by trees. Master craftsman Sathyan Edathodi shared that the construction, normally completed within one to two years, had extended to five years due to delays caused by the COVID-19 pandemic. The ships finally set sail in November 2024.
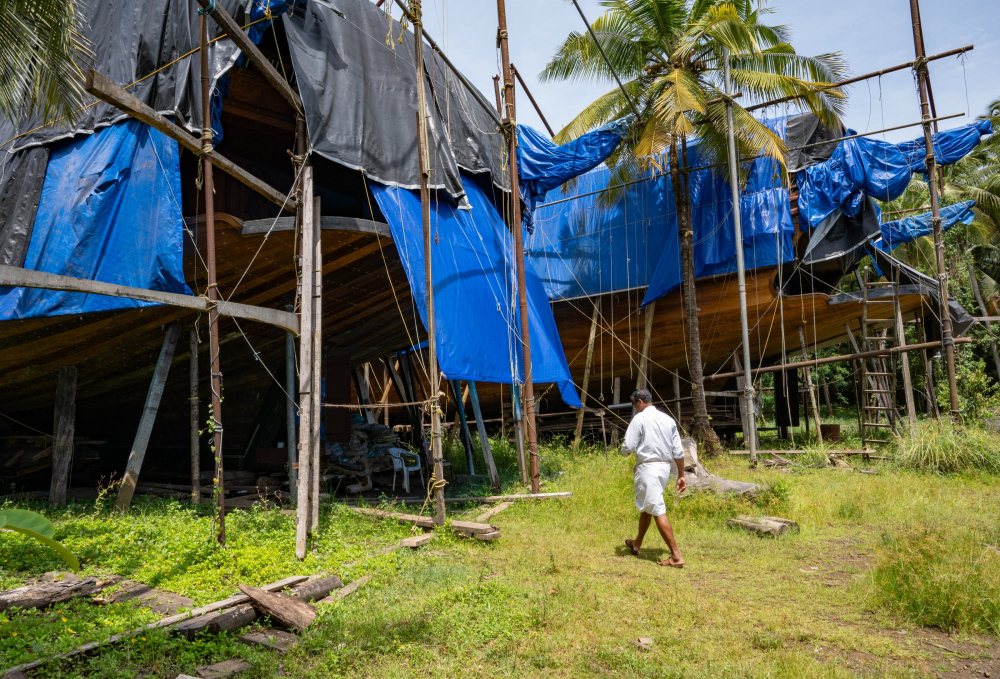
The uru under construction, covered with blue tarpaulin sheets. (Picture credits: Joseph Rahul)
These vessels are expected to outlast their creators—ships built by Edathodi’s late father, also an artisan, are still sailing after more than 75 years. Over time, Beypore’s boatyards have crafted a variety of urus, ranging from small to massive in size. The largest ship Edathodi has built stands 200 feet long and took three years to complete.
While urus historically played a vital role in the Indian Ocean trade, ferrying people and cargo, their modern purpose has shifted. Today, they are predominantly luxury vessels used for leisure. Building an uru is a significant investment and they are commissioned by royal families and businessmen from Gulf countries such as Qatar, Kuwait and Bahrain.
Crafted Through Indigenous Knowledge
The traditional techniques of shipbuilding in Beypore have remained largely consistent over the centuries, with minor changes in methods and materials. Depending on the ship’s size, a team of 10 to 30 artisans is required for its construction. Edathodi explains that his clients usually specify the length of the ship, which serves as the foundation for the rest of its dimensions. According to him, the width of the boat is generally one-third the length of the keel, while the height is half the width.
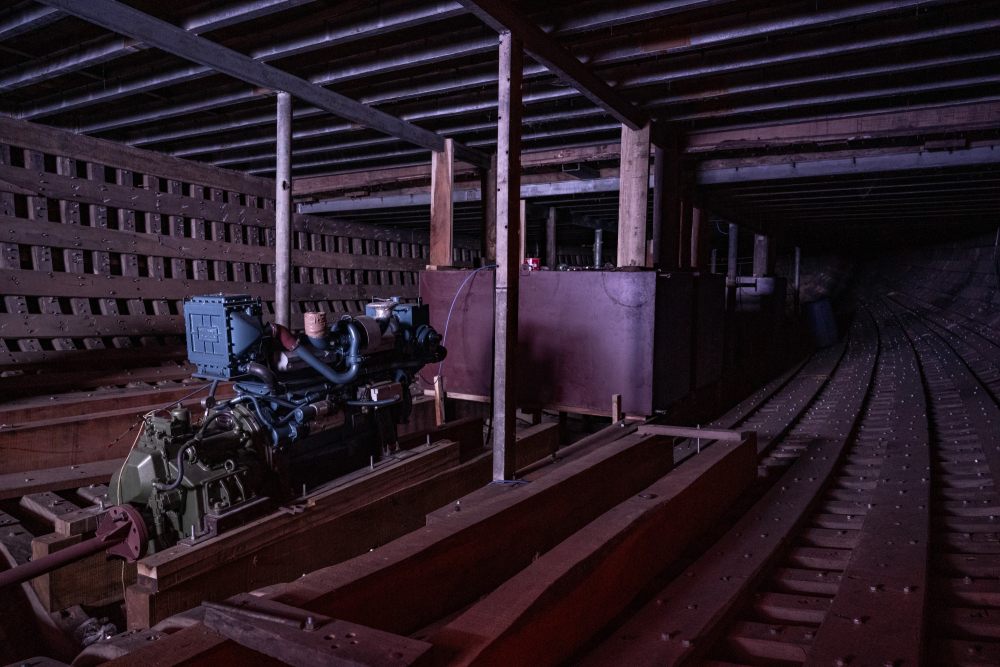
The engine inside the uru. (Picture credits: Joseph Rahul)
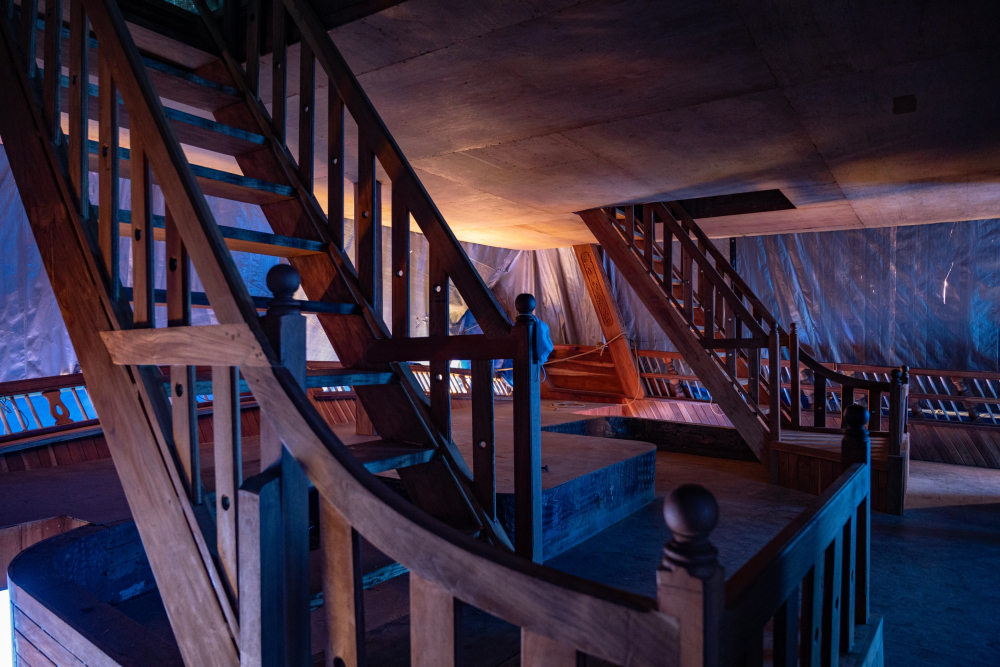
Stairs to the upper deck of the uru. (Picture credits: Joseph Rahul)
Also read | At the Ocean’s Crossroads
While today construction begins with a scaled sketch or a small wooden model, historically, urus were crafted without blueprints or plans, relying solely on the expertise and intuition of the artisan. At present, at the request of clients, marine engineers or architects are often involved. They use the model created by the master craftsman to develop a digital blueprint, which is professionally signed and sealed for approval.
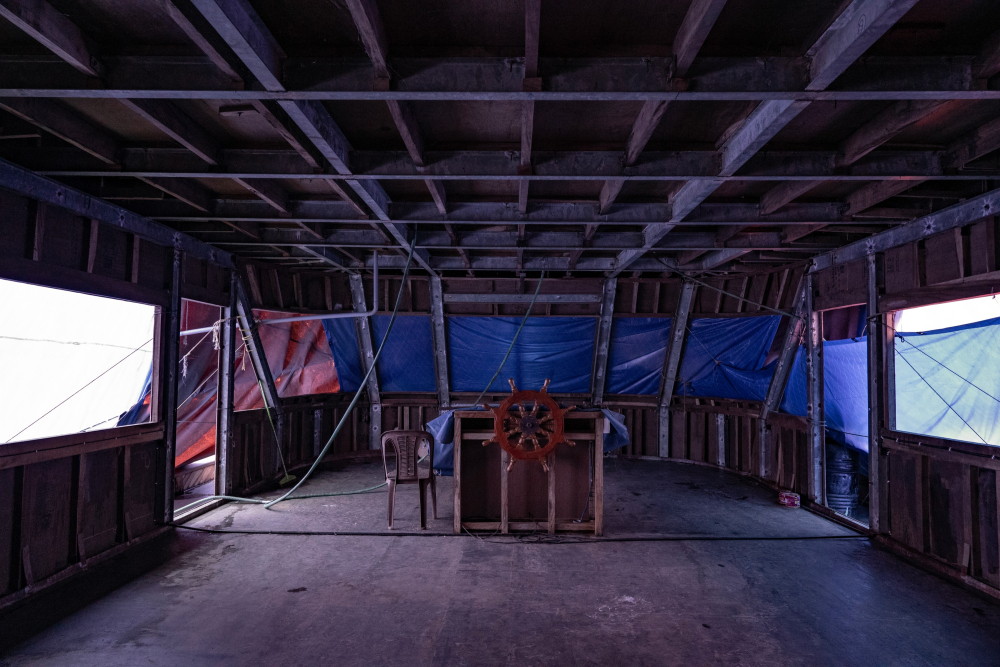
The main cabin whose interiors will be completed abroad. (Picture credits: Joseph Rahul)
Teak timber, sourced locally, was the primary material used in shipbuilding, along with timber of other indigenous woods available through the region’s thriving timber industry. Malabar was once a hub for exporting teak to the Arab coast. Logs were historically transported from upstream forests by floating them downriver, with a man or two steering the bundles. Elephants or bullock carts were used to move the timber to the river. At the yard, markings were made on timber using strings dipped in charcoal. The logs were placed on bars and cut using a long hand saw, operated by two men. Currently, due to environment-friendly regulations and cost considerations, imported timber from countries like Malaysia are widely used.
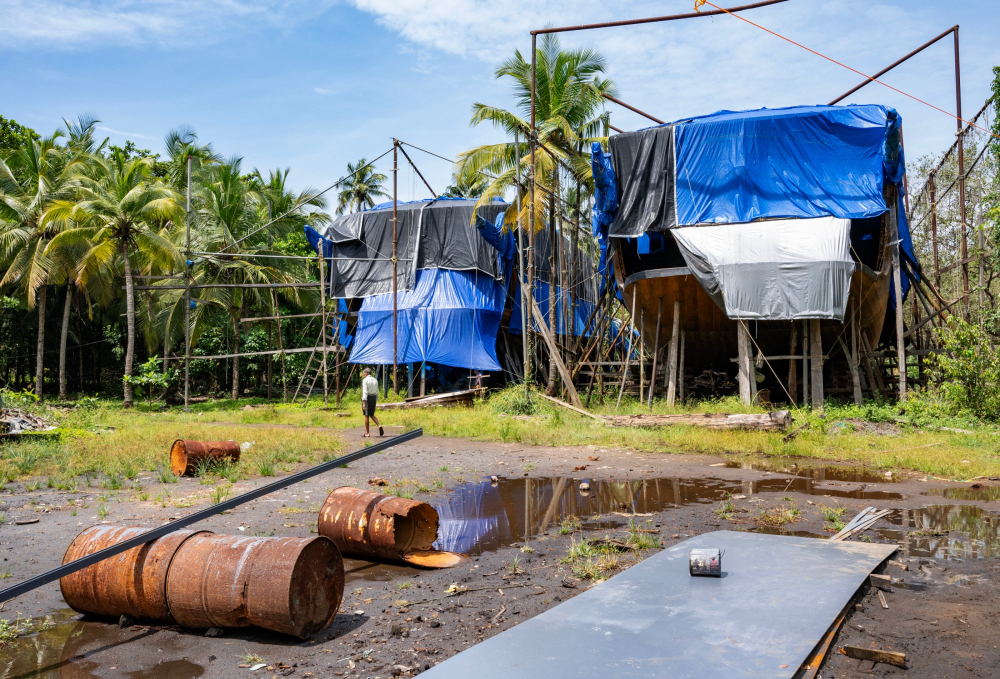
The uru under construction. (Picture credits: Joseph Rahul)
The keel, the backbone of the ship, runs along its length at the bottom, providing stability and structural integrity. Curved timbers are attached to the keel’s sides, the timber planks forming the frame of the ship’s body. In modern times, copper and zinc-coated iron nails of varying sizes are used to fasten the wood pieces. Before driving in the nails, the circular gaps are filled with cotton to ensure an airtight seal, as the wood swells over time to close the spaces.
Beypore’s strategic location has been a key factor in sustaining its shipbuilding tradition. It had easy access to essential materials, including diverse timbers, coconut coir ropes and fish oil.
Propelled by Trade and Migration
Another factor in the longevity of this industry is the skill and dedication of its artisan, labour and business communities. The traditional techniques of shipbuilding were honed and passed down orally through generations by the maesthiris. Edathodi recalls how his father was introduced to the craft by the Edathumpadikal family, one of the earliest maesthiri families in Beypore. When there was an overflow of work, the family employed other skilled artisans from the area.
The Khalasis, a native Muslim community, specialising in lifting heavy weights and equipment using just ropes, winches and pulleys, played a crucial role in the shipbuilding process. They were involved in every stage of uru construction—from transporting logs of timber from the river to the yard to launching the finished ships into the sea. The latter takes about a week of intense manual labour and draws large crowds, including local media.
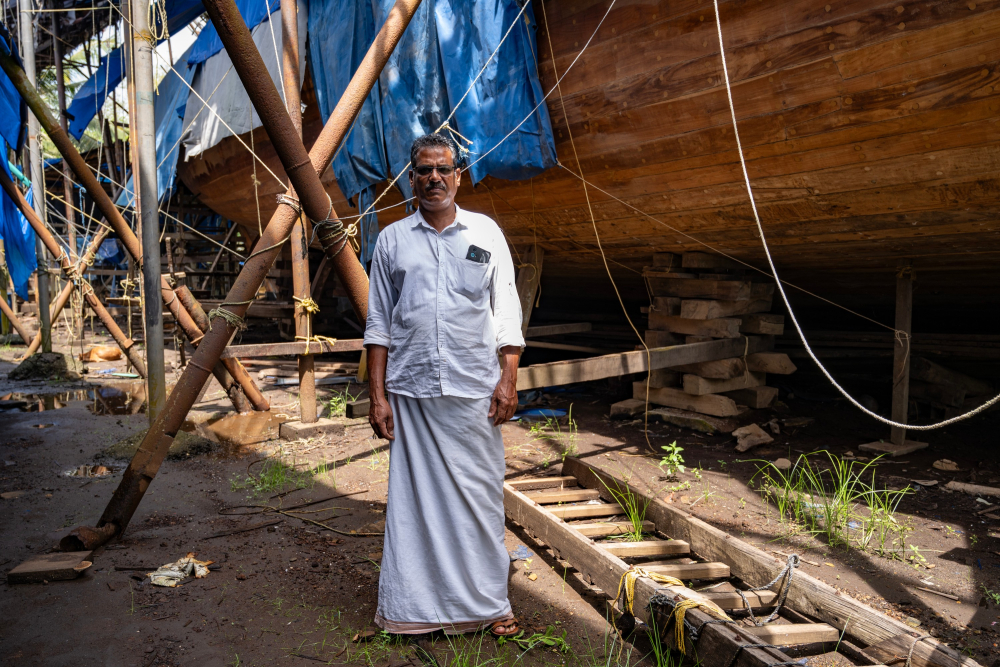
A portrait of Sathyan Edathodi. (Picture credits: Joseph Rahul)
The prominent businessmen who drove trade and shipbuilding in the nineteenth and twentieth centuries largely hailed from the Muslim community, whose ancestors had migrated to Kozhikode from the Gulf Peninsula. The surname Baramy is synonymous with the industry. The first Baramys, who migrated from Yemen, married locals, and their descendants became established traders. Similarly, the Koyas were also heavily involved as agents in both trade and shipbuilding.
Tradition at the Helm
The cultural significance of the uru is undeniable, yet the industry’s potential remains largely untapped. A few years ago, the government established a training institute in Beypore to support the craft, but it was abruptly shut down due to a lack of interest and resources. Edathodi believes that formal education or certification would be crucial to sustaining the craft. ‘We are willing to teach without remuneration. In the end, recognition is what matters,’ he says.
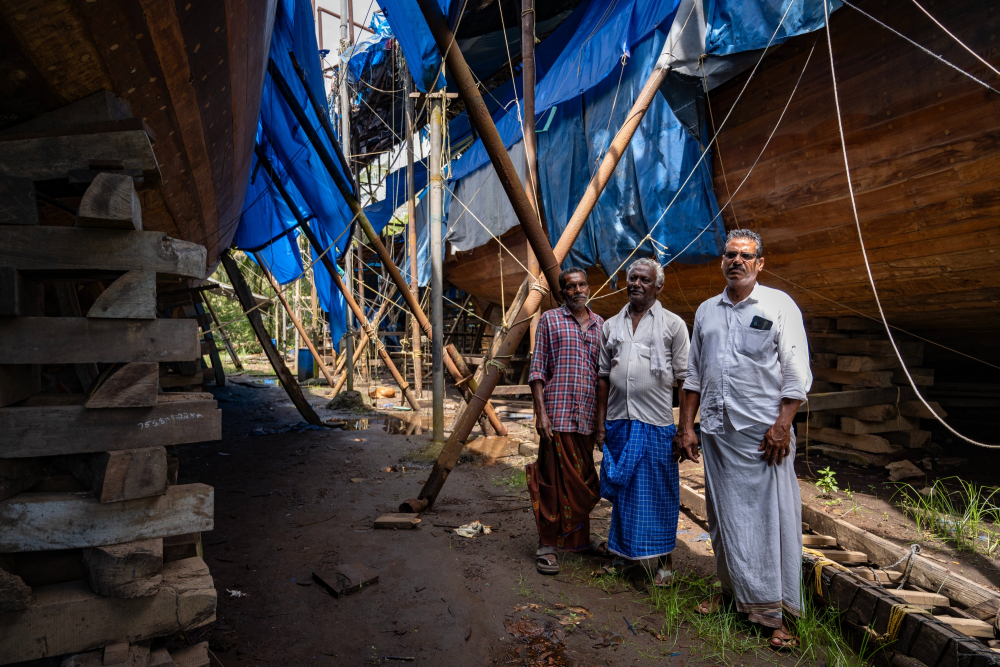
Sathyan Edathodi with his main craftsman at the boatyard. (Picture credits: Joseph Rahul)
Private entrepreneurship may hold the key to the future. For example, the Dhow Museum in Kozhikode, dedicated to preserving the legacy of the uru, is managed by a private shipbuilding company founded in 1885 by Kamakantakath Kunhammed Koya Haji. Operating the second boatyard in Beypore, the company has seen success in recent years. The current generation is committed to informing future generations about the industry—the museum houses archival photographs, books, records and other artefacts related to the craft.
The uru also presents a sustainable alternative and holds immense potential for tourism. However, success is not guaranteed, and genuine efforts will be required to ensure its growth. Edathodi, who began working in 1983, is well aware that he will be the last in his family to build ships; his son is currently working in a bank. While the future of the uru industry remains uncertain, Beypore continues to send its urus to sea, as it has done for centuries.
This essay has been created as part of Sahapedia's My City My Heritage project, supported by the InterGlobe Foundation (IGF).