The production of paper, fuelled by its growing demand as a medium for record-keeping and communication, spread throughout northern India under the Delhi Sultanates from the thirteenth century onwards. As the craft of papermaking flourished, paper gradually replaced traditional materials such as birch bark, cloth, palm leaves and so on. Artisans known as kagazis—a term derived from the Persian kagaz (paper)—settled near capital cities and commercial centres, where they produced paper by hand using materials such as cloth rags, hemp and jute fibres.
The Artisans of Kagzipura
The Kagzipura village located in Aurangabad—its name combining kagazi (those who made paper) and pura (settlement)—is home to a centuries-old artisan community whose ancestors arrived in the region in 1327 during Delhi Sultanate ruler Muhammad bin Tughlaq ambitious relocation of his capital from Delhi to Devagiri (renamed Daulatabad) in present-day Maharashtra. Among the many professionals who accompanied this large-scale migration were papermakers—artisans whose skills were in demand, as paper was not readily available in the region at the time.
However, the move was short-lived. In 1335, when Tughlaq returned to Delhi, many migrants, including from the community of kagazis, chose to stay on. They eventually settled in a village about 4 kilometres from Daulatabad, naming it Kagzipura. Today, the village lies in the Khuldabad Tehsil of Chhatrapati Sambhajinagar district, approximately 21 kilometres from the city.
Papermaking continued through the centuries in Kagzipura, and by the latter half of the twentieth century, nearly every house in the village functioned as a kaarkhana (workshop). Traditionally, the entirely manual process of papermaking utilised cotton, san (hemp fibres) and jhaal (tree bark), though the latter is no longer considered environmentally sustainable. Kai (moss) from lakes was also used, producing a paper of superior quality. Without electricity, raw materials were heated over a fire for two days before being beaten and scrubbed into a pulp.
A significant shift occurred in 1954 with the establishment of the Handmade Paper Manufacturing Society, which brought structure to the local industry and eased competition among village artisans. Mohammad Altaf, a 52-year-old artisan from Kagzipura, comes from a family deeply rooted in the craft; his father, Mohammad Ibrahim, began working in the 1960s. Despite challenges, such as the 1972 water shortage and recurring droughts over the decades, papermaking persisted. Altaf recalls the village gaining wider attention, particularly in the 1980s, when film stars like Dilip Kumar and Saira Banu visited the area.
However, as the paper industry rapidly modernised, cheaper machine-made alternatives turned handmade paper into a luxury and a fading craft. ‘This is a flawed business. The cost of making handmade paper is high, but the demand doesn’t match. It is also more expensive than mass-produced paper—a handmade paper diary costs significantly more than regular diaries in the market. Financial struggles have always been a part of this trade,’ says Altaf.
The declining demand and financial hardships ultimately led to the collapse of the village’s paper industry in 2007. Artisans who had relied on the craft for generations were forced to seek alternative livelihoods, turning to wheat bhattis (mills), dairy farming, transportation and other trades to sustain themselves.
A Recent Revival
In 2017, Kagzipura’s papermaking craft was revived through a joint initiative by the Cosmo Foundation—the CSR arm of Delhi-based Cosmo First Limited—and the Indian National Trust for Art and Cultural Heritage (INTACH) through its local chapter. The project aimed to develop Kagzipura as a modern heritage village, not only by establishing and supporting a paper mill but also by improving infrastructure and education.
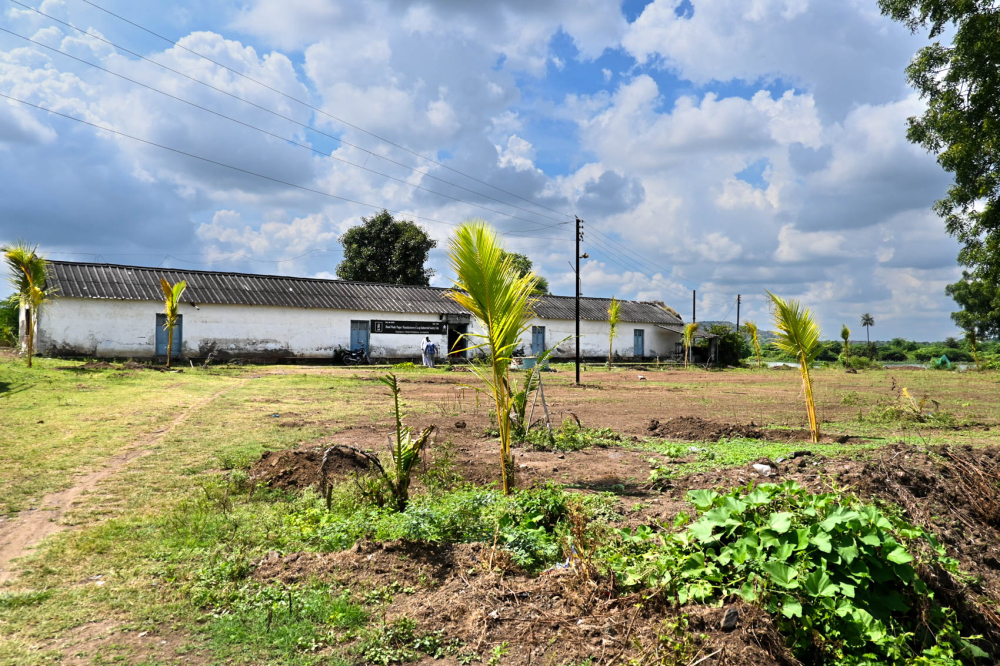
Paper mill reopened in 2017. (Picture Credits: Anil Purohit)
The Foundation introduced several school programmes such as Computer Operation and Digital Skill Building, Basic English Fluency Development and Cosmo Gyan Vihar Kendra for special learners. Sustainability efforts included rainwater harvesting, an underground water filtration and sewage treatment plant (STP) system, and the installation of public waste disposal systems. The on-ground implementation of these initiatives is overseen by Rajat Bathe, the CSR Coordinator, and Lakshmikant Mankar, the Cluster Coordinator.
The initiative also manages various aspects of the paper mill’s operations, including artisan and labour payments, machinery maintenance, material procurement and product sales. The installation of a solar power system has cut electricity costs by INR 3,000 per month.
When production resumed, Altaf rejoined as an artisan alongside Gawas Khan, a veteran artisan who had worked alongside Altaf’s father. Among the younger artisans is Sameer Sheikh, whose grandfather, Azimudeen Sheikh, was once part of the industry. As a child, Sameer often accompanied his grandfather to the workshop, and when the mill reopened in 2017, he, too, became a part of it. Sheikh fondly recalls an unusual moment when the popular crime show C.I.D. filmed in the village, ‘The story involved retrieving a piece of paper from a dead body and the investigation that followed.’ Today, the mill employs around 10 people, including artisans and helpers.
However, few villagers are willing to take up papermaking as a profession, as wages remain lower compared to other industries. With Daulatabad Fort and the Ellora and Ajanta Caves nearby, some young people from the village are even training for careers in tourism. This could also open opportunities for visitors to engage with the village’s paper mill. Currently, most paper products are sold through exhibitions and other limited avenues, but integrating tourism could help boost sales. Another key challenge is knowledge transfer—only a few artisans from the older generation experienced in traditional papermaking techniques remain.
The Craft and Toil of Papermaking
‘My favorite type of paper is one where we embed flower petals or neem leaves between two layers of pulp and press them into a single sheet,’ says Sheikh. Holding up a sheet to the sunlight, he points out the delicate dried petals, their shapes visible in a subtle contrast against the white paper.
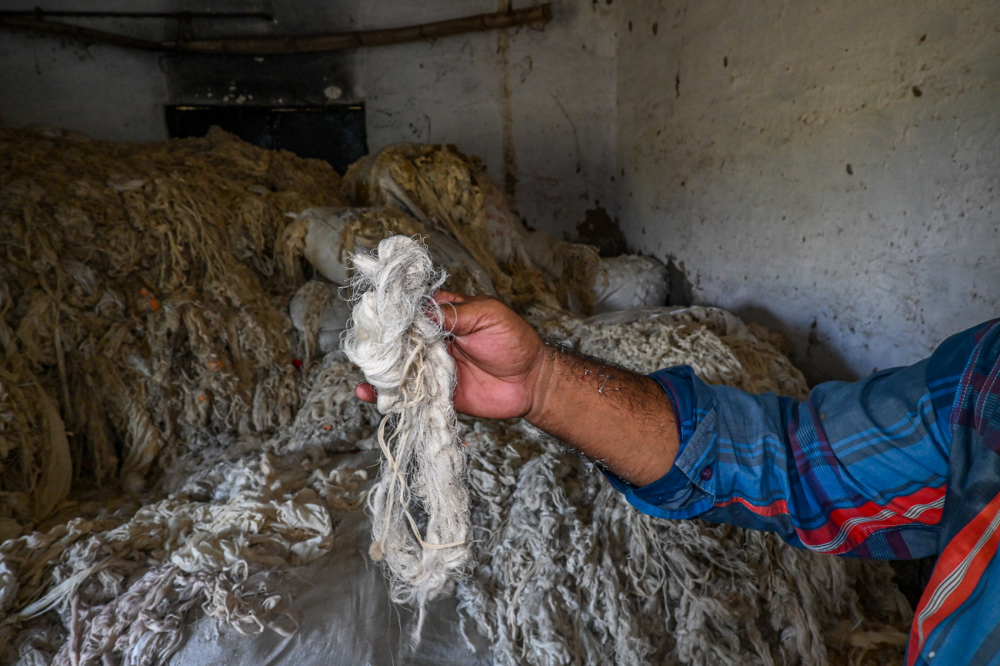
Cotton thread used as raw material. (Picture Credits: Anil Purohit)
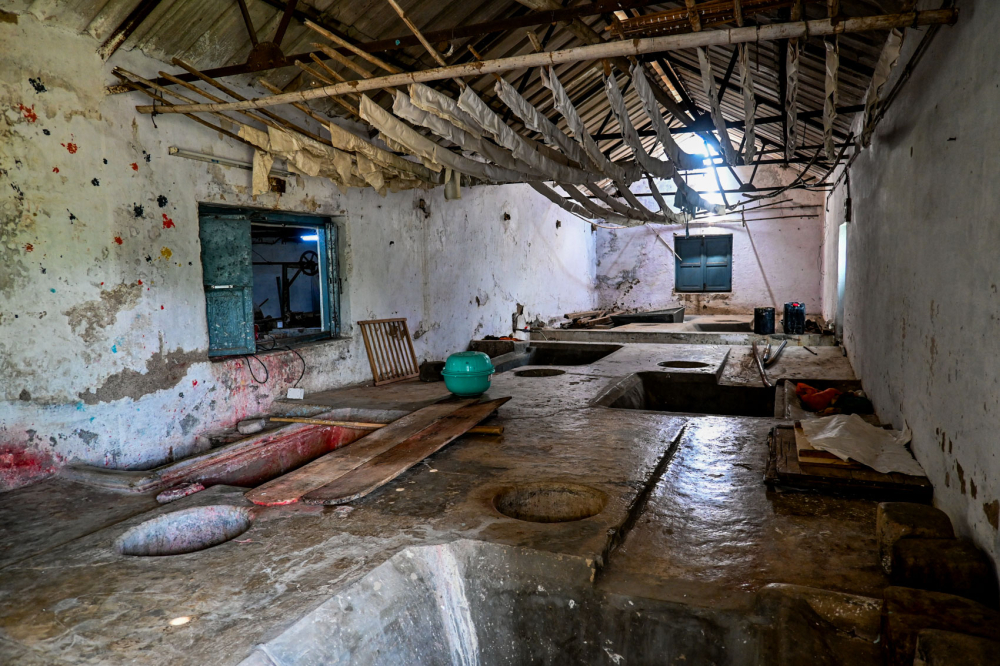
Interior of the paper mill, featuring pits used for processing raw materials and areas where paper is laid out to dry after pressing. (Picture Credits: Anil Purohit)
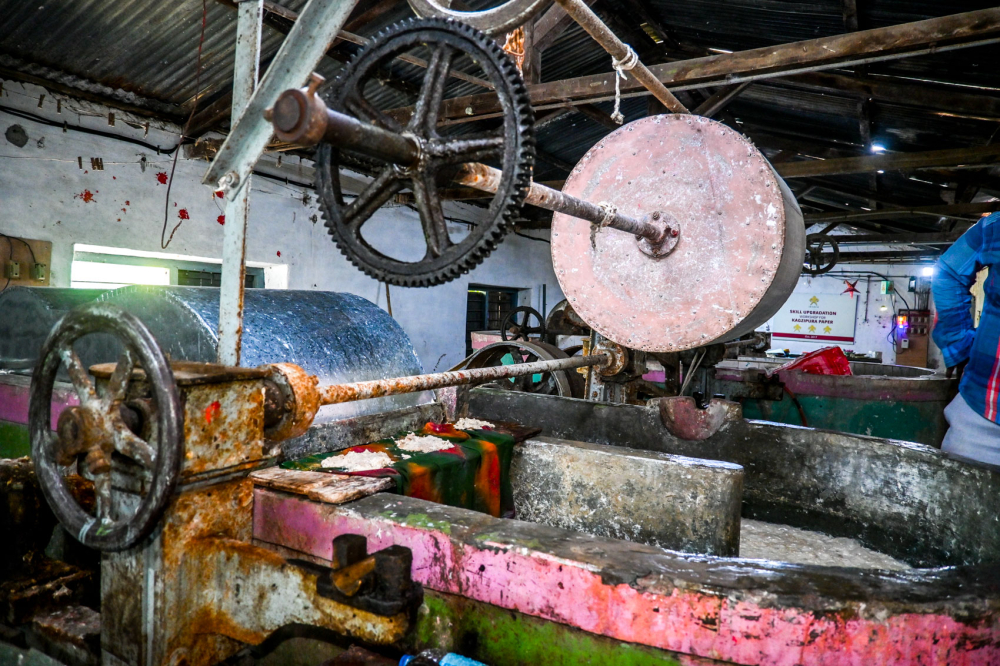
Mixer machine. (Picture Credits: Anil Purohit)
Producing a sheet of paper, usually part of a batch of 60, takes approximately eight hours. The process begins with 30 kg of cotton thread, which is processed in a mixer machine for five to six hours. Water is periodically added to clean the cotton and create a pulp. Initially, only the cotton thread is churned, after which bleaching powder is introduced. The contaminated water is then drained, replaced with fresh water and mixed again. To ensure the paper holds ink without smudging, fitkari (alum) and a binding chemical are added. Natural dyes such as henna and turmeric, or fabric colours, may also be mixed in to create tinted paper. Approximately 750 sheets of paper can be produced from 30 kg of cotton.
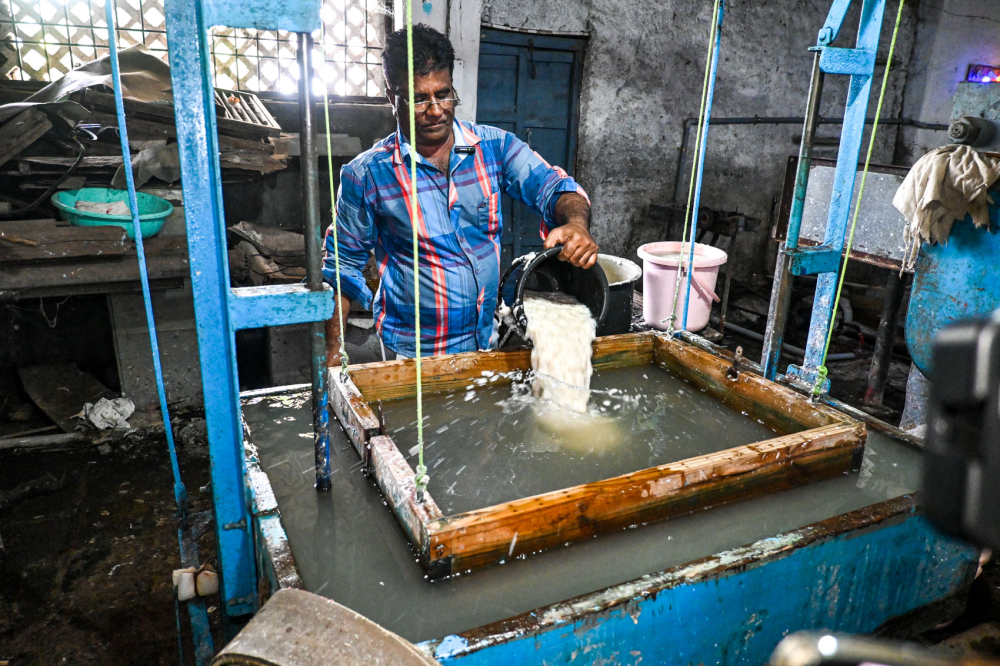
Mohammad Altaf pours the pulp into the frame of the vico vat machine which is operated by hand. (Picture Credits: Anil Purohit)
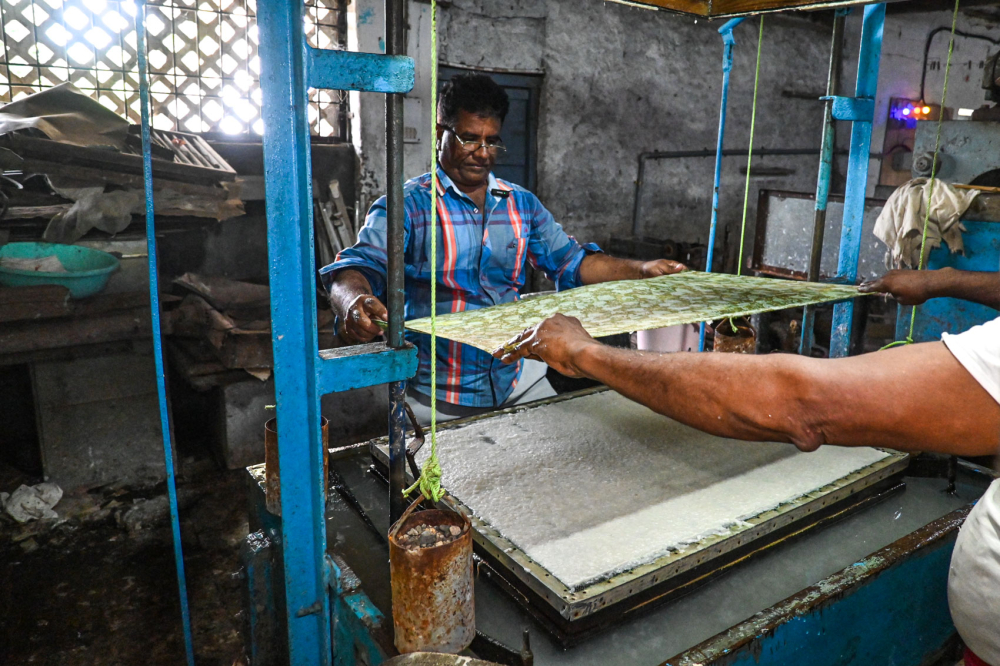
Mohammad Altaf lifts the frame to drain water. (Picture Credits: Anil Purohit)
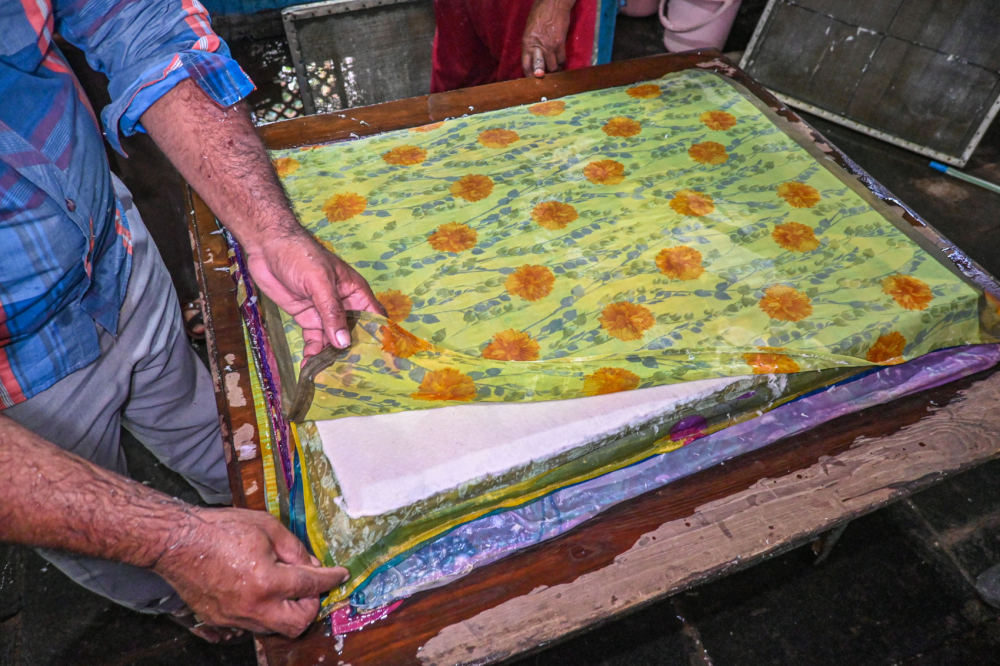
Artisans separate layers of pulp with cloth. (Picture Credits: Anil Purohit)
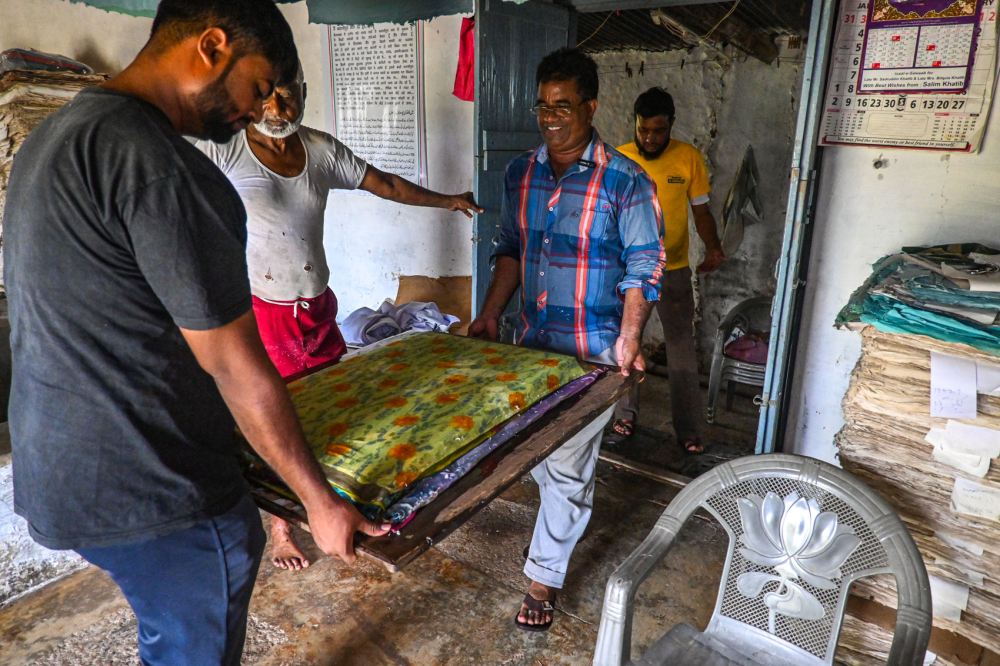
Mohammad Altaf and Sameer Sheikh carry the layers to the press machine. (Picture Credits: Anil Purohit)
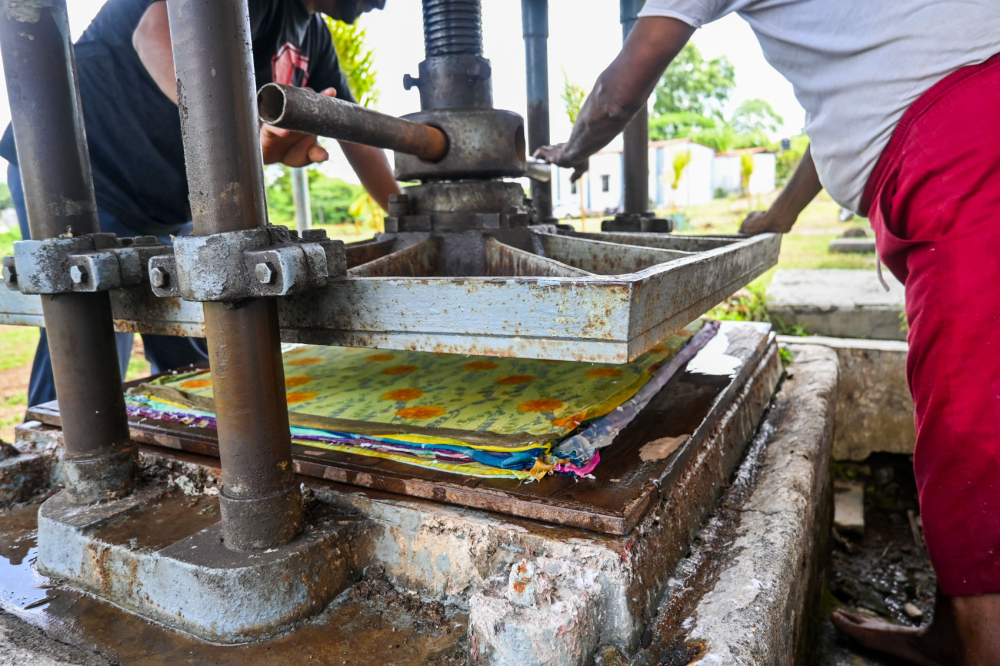
Press machine being operated. (Picture Credits: Anil Purohit)
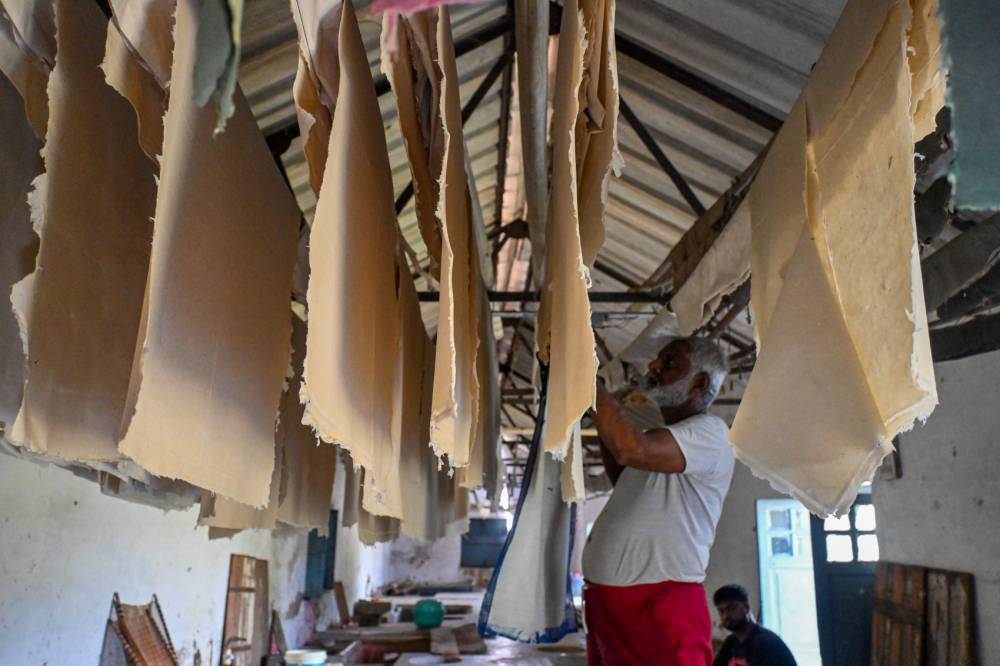
Paper sheets are hung out to dry after using the press machine. (Picture Credits: Anil Purohit)
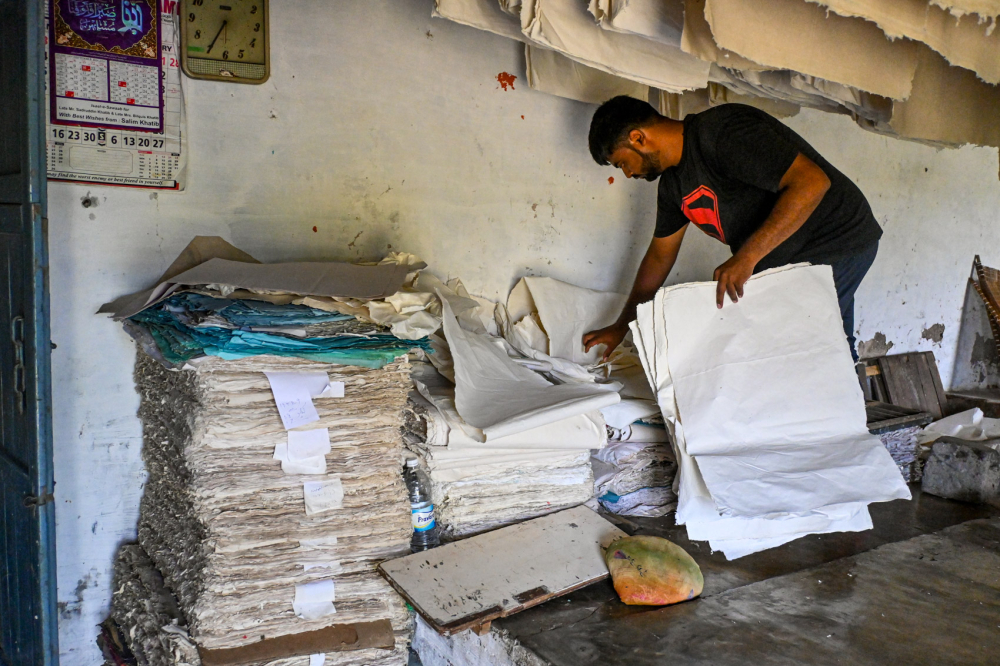
Paper bundles. (Picture Credits: Anil Purohit)
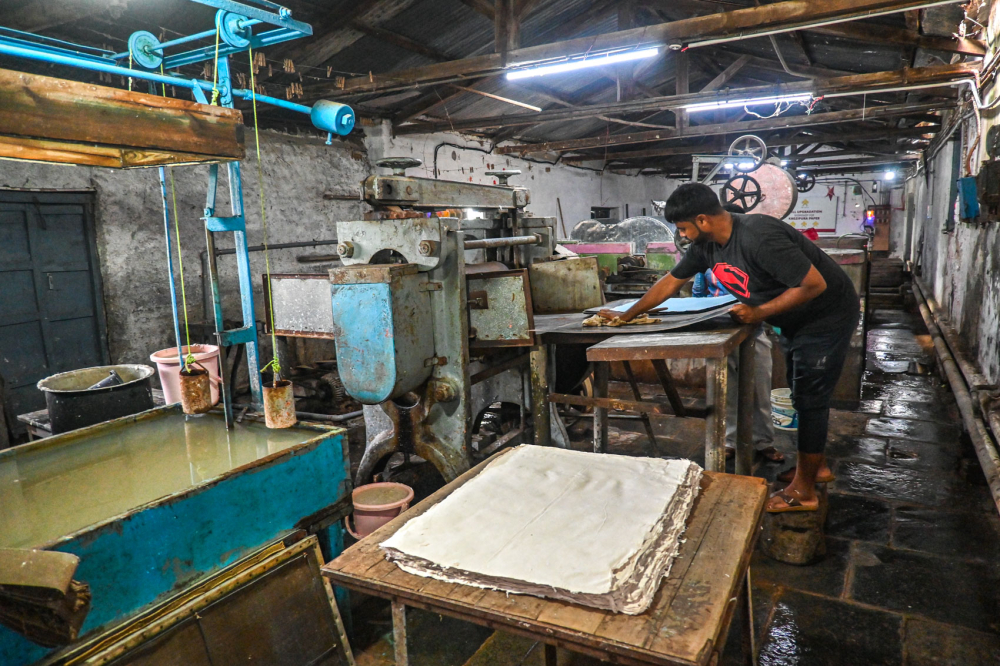
Sameer Sheikh demonstrated how paper is straightened. (Picture Credits: Anil Purohit)

Sameer Sheikh demonstrated how paper is straightened. (Picture Credits: Anil Purohit)
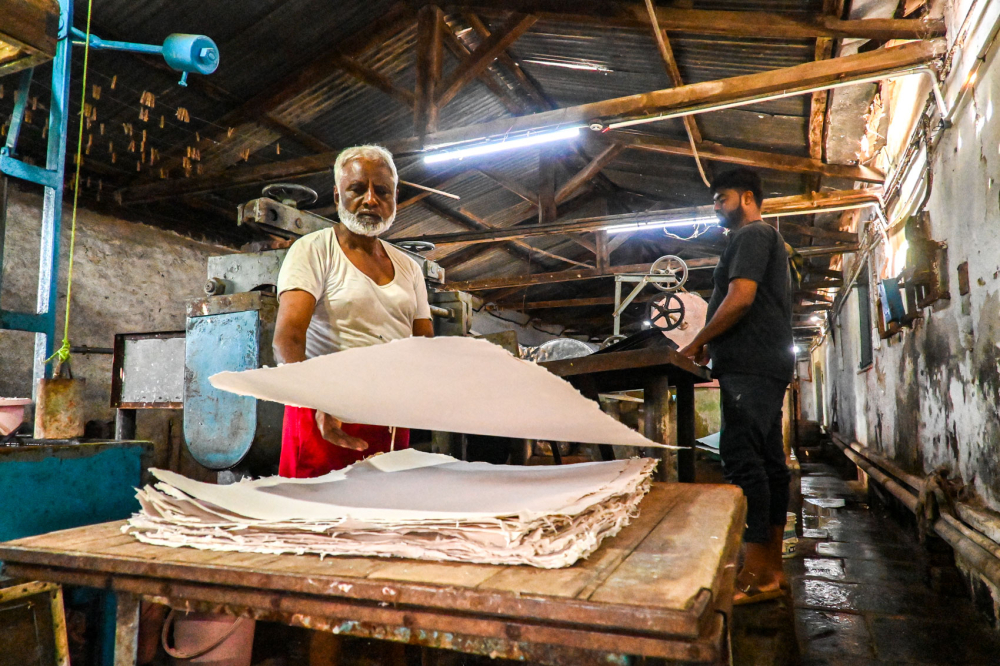
Gawas Khan stacks paper that was straightened and cut. (Picture Credits: Anil Purohit)
Once the pulp is ready, the artisans begin work on the Vico Vat machine, which is operated manually. Using intuition to gauge the right quantity, a layer of pulp is poured into a wooden frame with a mesh screen, and carefully washed by hand to remove any lumps or impurities. The frame, suspended from the ceiling by nylon ropes, is then swung gently to drain excess water, leaving behind an even layer of pulp. The standard frame size is 34 x 24 inches, but with dividers in place, it can produce four sheets measuring 16 x 12 inches each.
After draining, the frame is removed from the machine and tilted to release additional water. A thin cloth is placed over the pulp layer to keep it intact. The frame is then flipped upside down onto a table, with the cloth at the bottom, and pressed down by hand—usually by two people working together. Once a stack of at least 60 pulp layers, each separated by cloth, is ready, it is taken to a press machine outside the mill, where it is compressed into paper sheets. The final sheets are cut evenly using a manually operated cutting machine. Most of the equipment used in the process is old, and since few technicians are familiar with these machines, the artisans often carry out repairs themselves.

Products created from handmade paper. (Picture Credits: Anil Purohit)
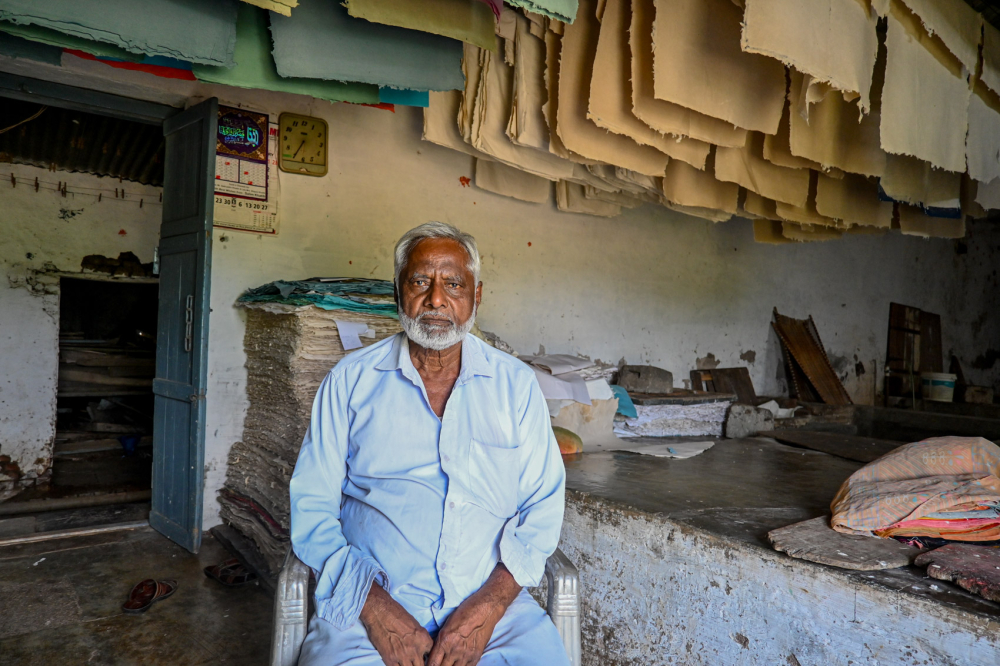
Gawas Khan. (Picture Credits: Anil Purohit)
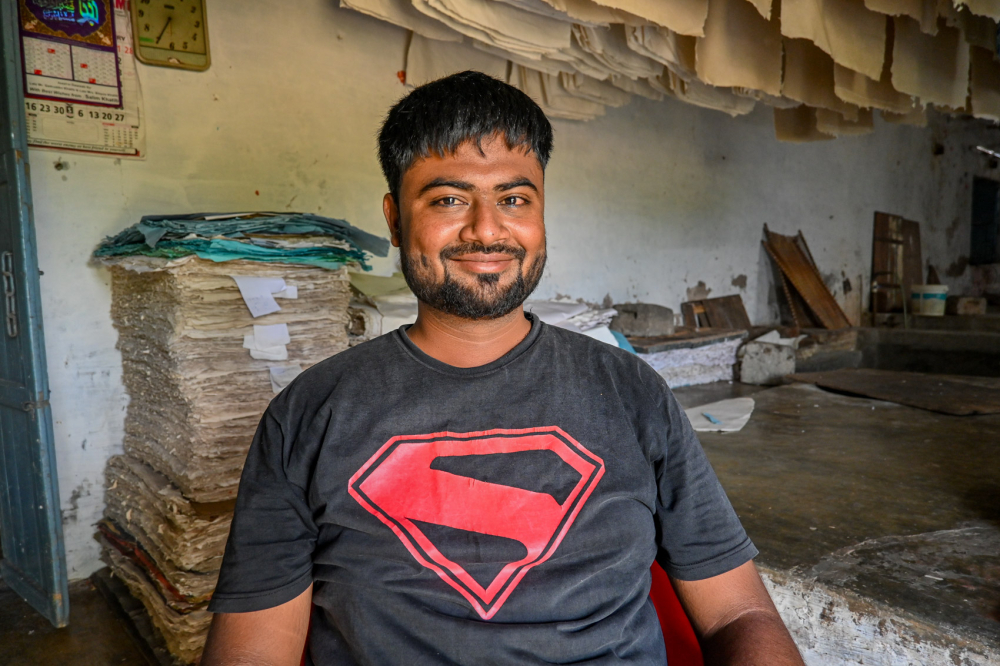
Sameer Sheikh. (Picture Credits: Anil Purohit)
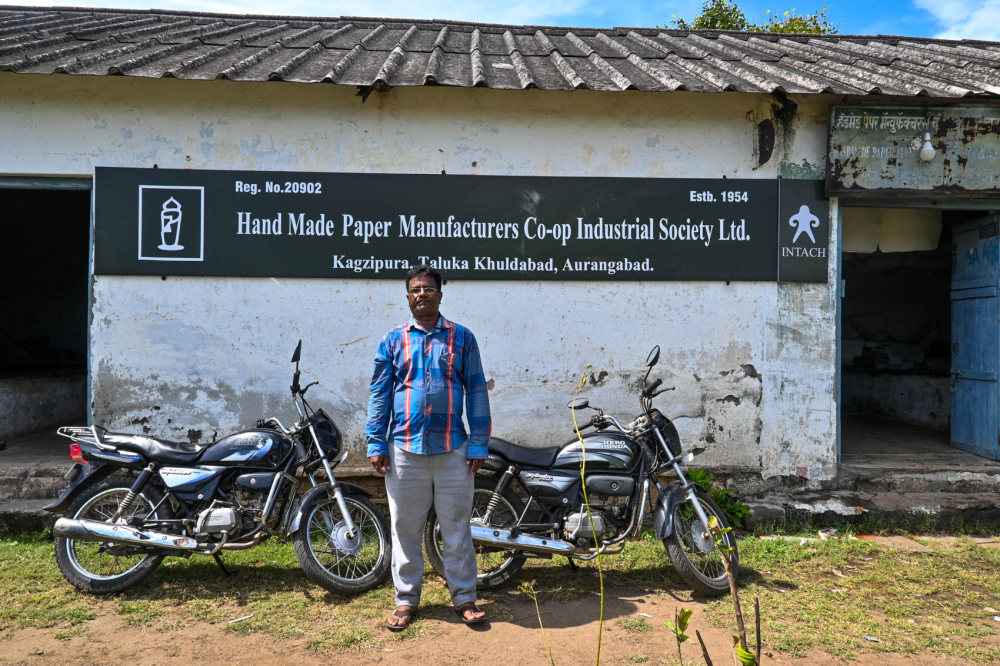
Mohammad Altaf outside the paper mill. (Picture Credits: Anil Purohit)
‘The quality of this handmade paper is excellent—its lifespan exceeds 100 years. The oldest sheet we have here is around 50 years old,’ says Altaf proudly. Despite its durability, handmade paper remains a niche interest, with few willing to invest in it for daily use. Artisans like Sheikh may be the last generation in the village to practice this craft. For now, the revival project in Kagzipura has kept the tradition alive, and the artisans take pride in their work and continue despite the challenges. Their greatest reward is seeing the craft recognised and respected. It is only fair that the long tradition of papermaking in the region is recorded in the pages of history with the same care that goes into creating each sheet of handmade paper.
This essay has been created as part of Sahapedia's My City My Heritage project, supported by the InterGlobe Foundation (IGF).